Unlocking Massive Savings: The Power of Steam Trap Monitoring
Steam, a vital resource in industrial processes, demands efficient management to optimize operations and minimize costs. A cornerstone of this efficiency is the steam trap, a device responsible for removing condensate and non-condensable gases from steam systems. However, the performance of these seemingly small components can have a significant impact on overall system efficiency and environmental impact.
The High Cost of Inefficient Steam Traps
When steam traps malfunction, the consequences can be severe. Failed-shut traps can lead to:
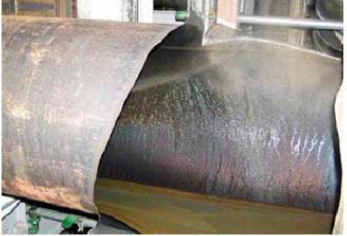
- Water hammer: Damaging equipment due to trapped liquid slugging.
- Reduced efficiency: Impaired heat transfer and potential equipment failure.
- Pressure surges: Causing system instability and safety risks.
On the other hand, failed-open traps waste vast amounts of energy, resulting in:
- Increased fuel costs: Inefficient steam usage drives up energy bills.
- Higher boiler loads: Additional strain on boiler systems due to increased steam demand.
- Environmental impact: Elevated carbon dioxide emissions from increased fuel consumption.
To illustrate the financial impact of a failed-open steam trap, consider this:
A single trap leaking 391 lbm/hr of steam can cost a facility over $34,000 annually. **
The Benefits of Steam Trap Monitoring
Implementing a robust steam trap monitoring system is essential for optimizing system performance and reducing costs. By continuously monitoring steam trap operation, facilities can:
- Identify issues early: Detect failing traps before they cause significant damage.
- Reduce energy consumption: Optimize steam usage and lower utility bills.
- Lower carbon footprint: Contribute to environmental sustainability by reducing emissions.
- Minimize maintenance costs: Prevent unplanned downtime and costly repairs.

Key components of an effective steam trap monitoring program include:
- Real-time monitoring: Using wireless transmitters to track trap performance.
- Regular inspections: Conducting manual surveys to identify potential issues.
- Prioritization: Identifying critical traps for focused monitoring.
- Proactive maintenance: Addressing issues promptly to prevent failures.
By investing in steam trap monitoring, businesses can achieve substantial cost savings, improve operational efficiency, and reduce their environmental impact.
Ready to optimize your steam system? Contact ESI Technologies Group today to learn how our advanced monitoring solutions can help you unlock the full potential of your steam system.
**If we take the example of a steam trap operating on a 100psi steam system with an
internal orifice of 3/8 inches, we can calculate the steam loss through a blow-through
or failed-open trap.
W = 24.24 x Pabs x D2
W = 24.24 x (100 psi + 14.7 psi) x (3/8)2
W = 391 lbm/hr
We can then apply the cost of steam for a process unit to find the financial impact of
a blow-through trap. A typical cost of steam is $10/1,000lbm.
Cost ($/yr) = Steam Loss (lbm/hr) x Cost of Steam ($/1,000 lbm) x 8,760 (hrs/yr)
Cost ($/yr) = 391 lbm/hr x $10/1,000 lbm x 8760 hr/yr
Cost = $34,250/yr
The cost of failing open for this particular steam trap is over $34,000/year.